Flow X-Axis Essentials
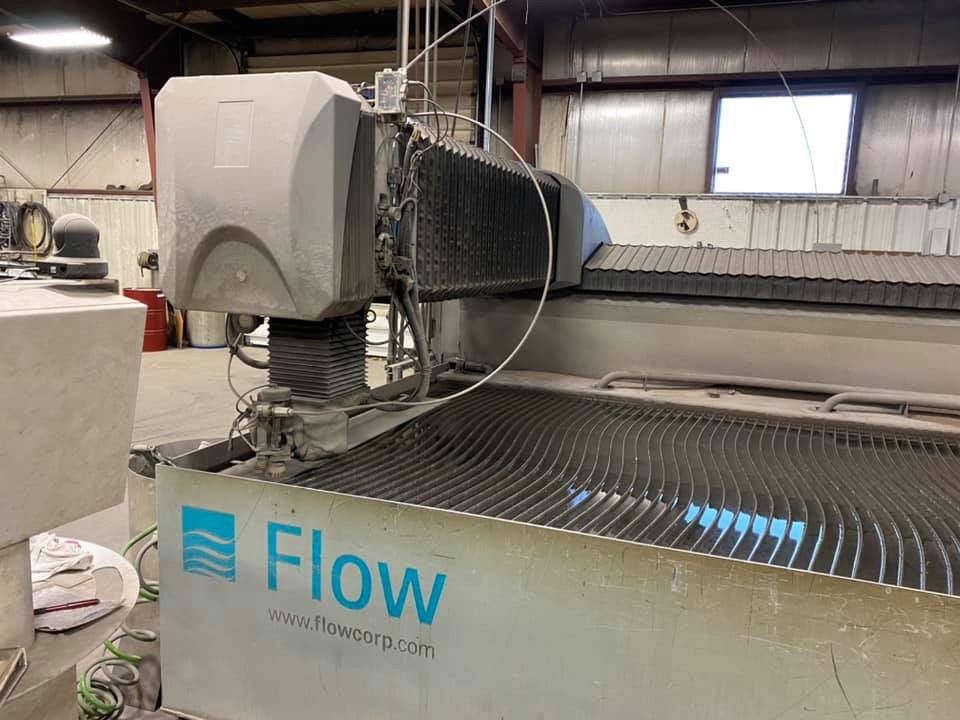
The most common design of Flow Water Jet Ballscrew Guys encounters is what we refer to as the “flying gantry” type. On these machines, the X-Axis moves an armature suspended over a cutting tank. Over the years Flow has made many different models and types. Some with a bigger or smaller tank. Some with a multi axis cutting head. Each often have specific repair nuances that must be observed. But for the most part, they share the same motion systems in concept. The most common call we receive about Flow Water Jets is that the X-Axis is loose or no longer performing to acceptable tolerances.
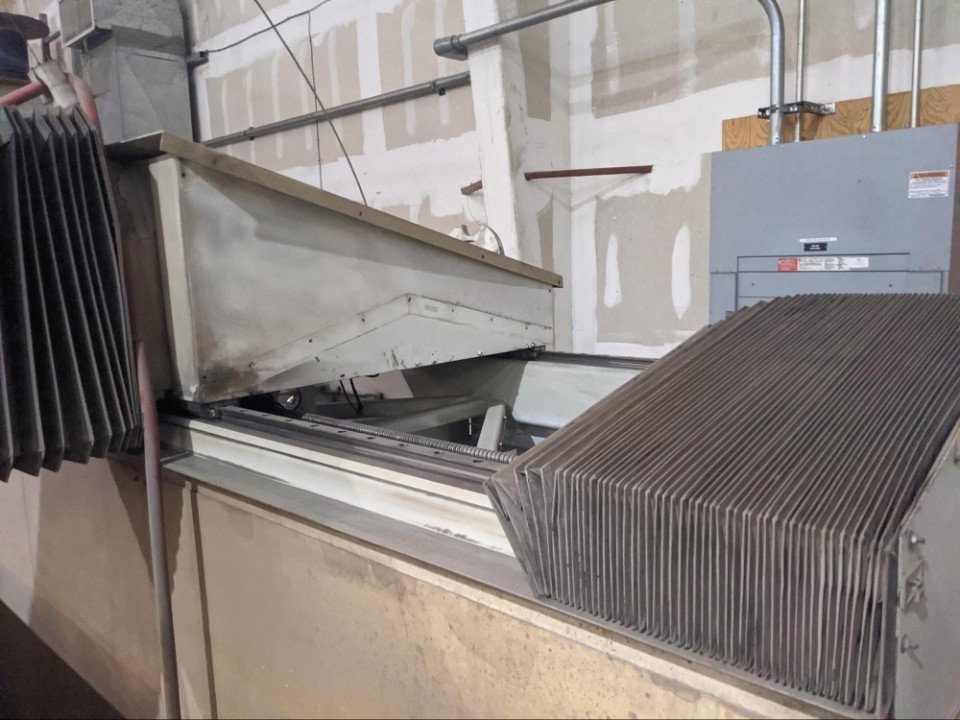
The first step in servicing the X-Axis is to remove the accordion covers and inspect them for any damage, such as cuts or holes. As anyone who works with a Flow Water Jet knows, the cutting media tends to migrate into every nook and cranny of the machine. One of the most common reasons for X-Axis failure is neglecting to clean and inspect the components regularly.
It's essential to keep the machine clean, and that includes the inside components. Underneath these covers are essential systems that require regular lubrication, including the linear way guide slider blocks. The grease fittings for these components are often obscured by the covers and can be overlooked during preventative maintenance.
As a service company, we understand the importance of regular maintenance and cleaning to ensure your Flow Water Jet operates smoothly and efficiently. By inspecting and maintaining the X-Axis components regularly, you can avoid costly repairs and downtime.
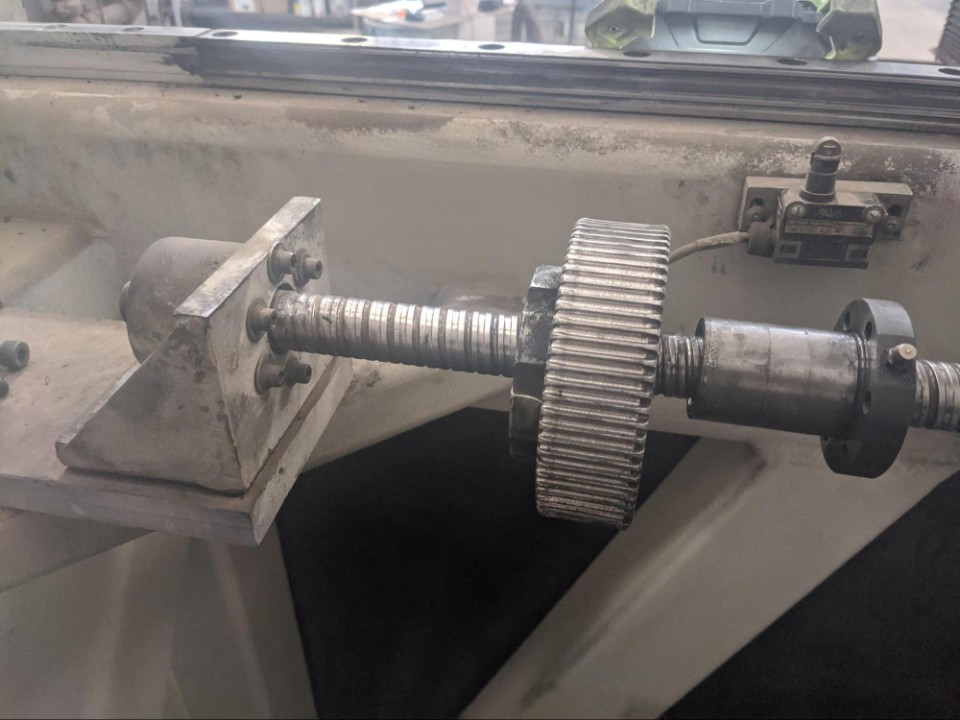
The next part of our Flow Water Jet X-Axis service is to disconnect the ball nut from the Y-Axis gantry. We remove the drive belt, inspecting the belt to make sure the teeth are in good shape. We also disconnect and examine the aluminum drive pulley for wear. The ball nut is also checked while still on the shaft. We evaluate if the seals are still keeping out debris, and checking to see if it has received regular lubrication. All are pulled off the ball screw shaft and completely cleaned.
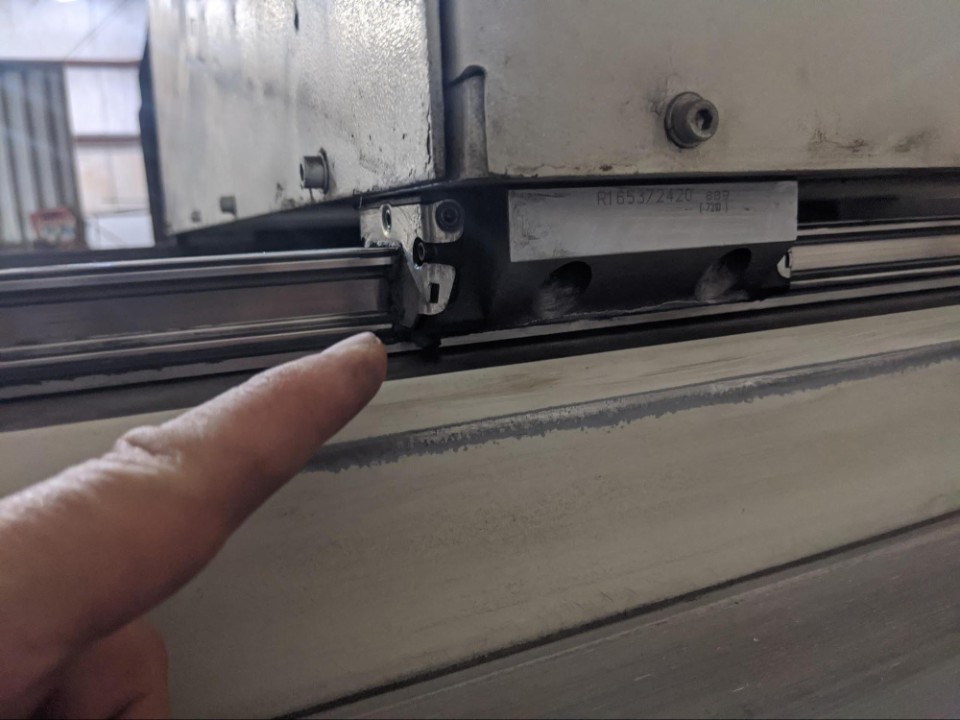
As part of our Flow Water Jet X-Axis service, we disconnect the ball nut assembly from the gantry and evaluate the linear way guide rails and slide blocks. We ensure that the entire cutting bridge can be moved effortlessly with one hand to check for clogged, poorly lubricated, or damaged ball bearing linear way guide slider blocks.
Different linear motion parts from various vendors, including Bosch Rexroth, INA, STAR, Thompson Linear, and Hiwin, have been used over the years in Flow equipment. Therefore, we assess the situation before demanding the replacement of both rails and slide blocks. Sometimes only the slide blocks need replacing, and if new slide blocks don't fit well on the rail, we may re-ball the linear way guide sliders with an oversized ball bearing to increase the preload and make a worn rail perform like new.
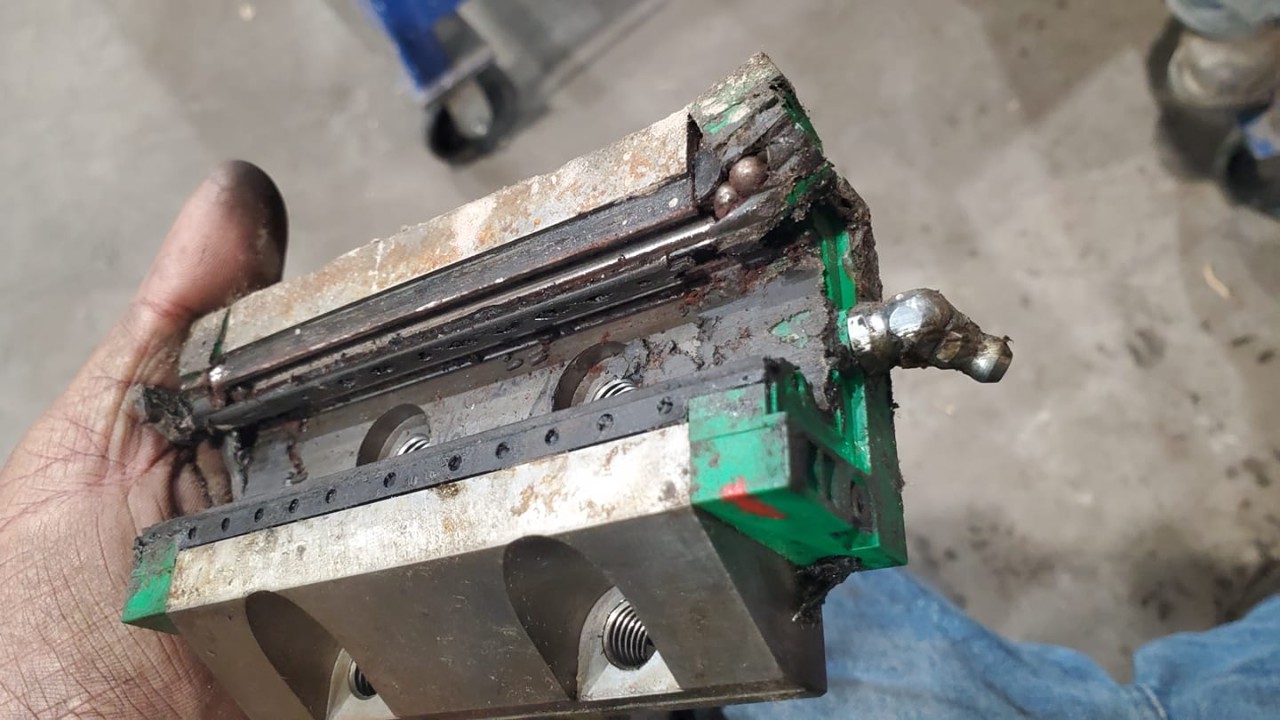
At times when we're called in to service the Flow Water Jet X-Axis, we encounter a common issue where the linear way guide slide blocks blow out on one side of the unit. The most frequent cause of this is the lack of lubrication, along with a buildup of dust, dirt, and cutting media debris. Over time, these blocks become clogged, rendering the four precision ball bearing tracks inside unable to roll and flow, ultimately causing the block to seize and fall. Although the Flow Water Jet may still be able to cut, you'll start to notice a jagged edge along your X-Axis straight away cuts, with holes becoming egg-shaped.
The worst part of this is that the ball nut begins to drag the cutting head gantry back and forth, resulting in wear on the ball screw assembly's acceleration. Over time, the ball screw may become loose, leading to a water jet with unacceptable parts. That's why it's essential to pull back the covers on your Flow Water Jet regularly. The blocks and rails need to be cleaned and lubricated. The specific Linear Way Guide slide block used is manufactured by INA, and at times it can be challenging to find them. Often, we've found that they have to be ordered from Europe when available, which may add downtime to your machine repair.
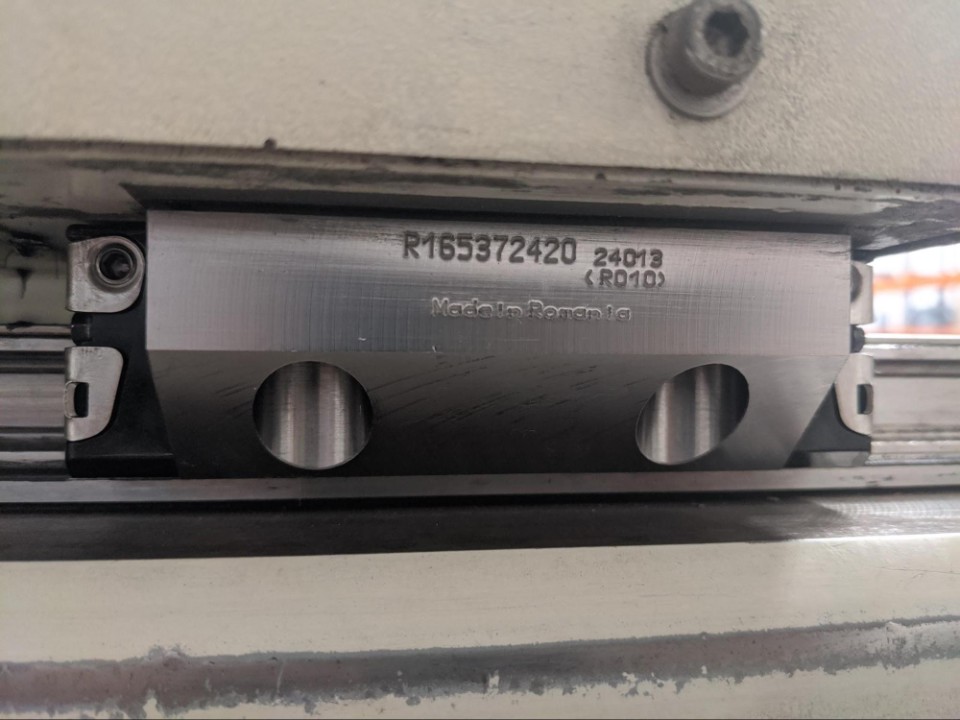
It's often possible to determine what kind of linear way guide block you have in your machine. Sometimes, the information is printed right on the side of the metal flange, while other times, it can be found on the plastic caps on either side of the block. Before we service your Flow Water Jet, we recommend that you check what kind of blocks are installed on your machine, so we can order them in advance and have them ready for field service.
We also encourage you to shop around for your own bearing parts and try to find a good deal. We don't add any markups and can help you find the parts you need. However, we do recommend that you always keep a spare pair of these blocks available at your facility as critical spare parts. In some cases, replacements may not be available for 4-6 months, so having a spare pair can help you avoid any downtime.
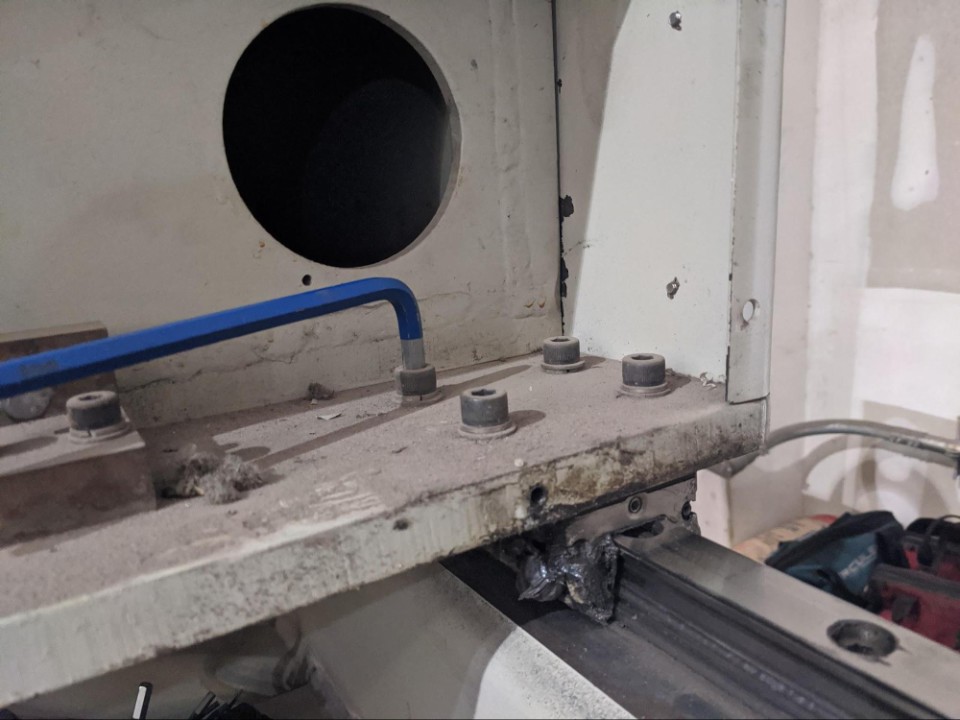
In this image, a damaged linear way guide block is being removed from the machine. Accessing the mounting bolts is relatively easy in some models of Flow Water Jet, as shown here. However, in most cases, these bolts can only be accessed from inside the cutting head gantry superstructure. This requires reaching your hand into the large diameter hole shown in the picture.
The boltheads inside are typically filled with debris and cutting media, which must be cleaned out with compressed air or a vacuum before attempting to remove the bolts. Otherwise, there is a risk of stripping the allen bolt heads, making the replacement of the linear way guide slide block even more challenging.
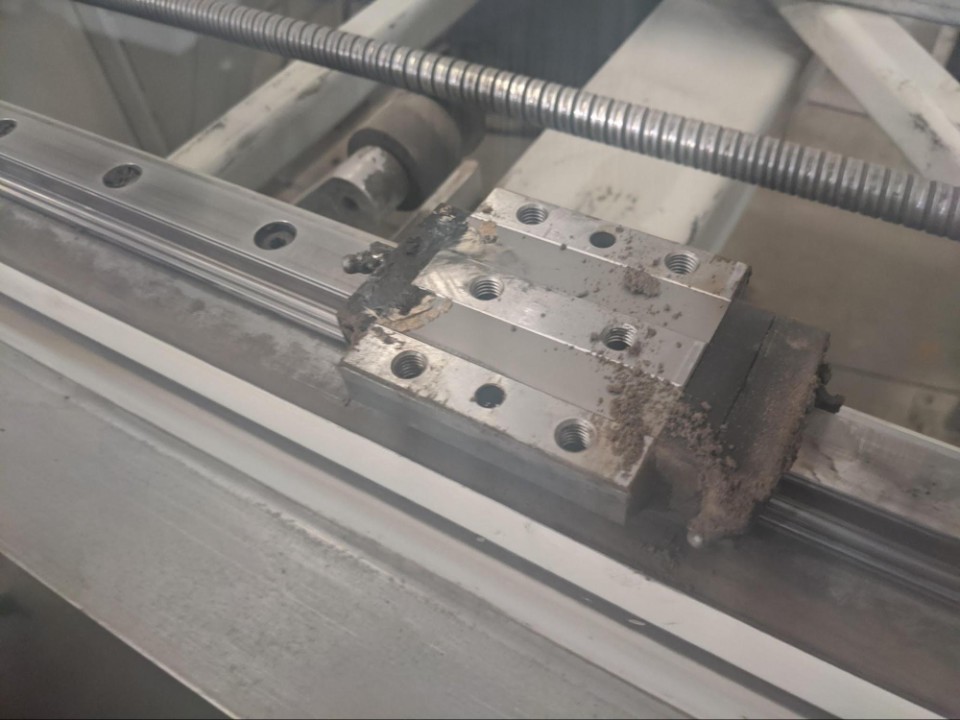
To ensure thorough Flow Water Jet X-Axis service, we remove every block from underneath the cutting head gantry. After cleaning the assembly, we check for any looseness or wiggle in the linear way guide blocks. Even if the ball screw is in great shape, four loose linear way guide blocks can result in 0.010" lost motion and slop in parts quality.
Loose linear way guide blocks can cause the cutting gantry to shimmy ever so slightly to different sides of the rail, resulting in poor cut anomalies in your parts. Therefore, it's essential to check and tighten these blocks during routine maintenance to ensure optimal machine function and high-quality part production.
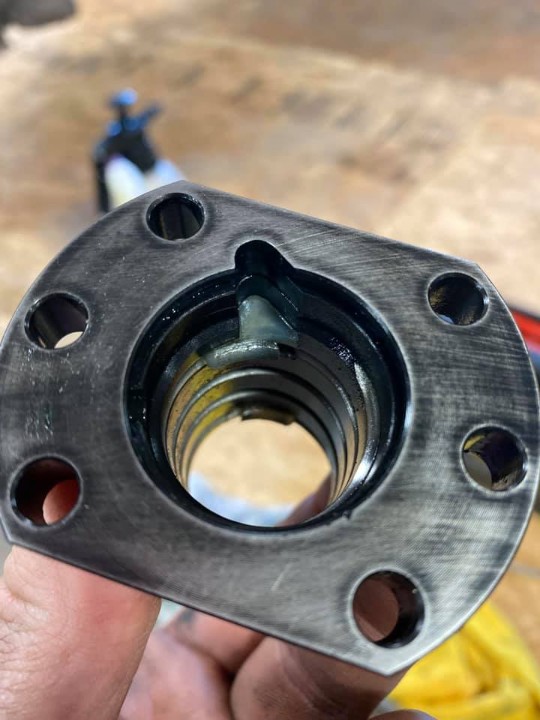
As a crucial component of the Flow Water Jet X Axis refurbishment, the ball nut is either rebuilt or replaced by our team. We have come across a wide variety of motion system parts in Flow Waterjets, with Bosch Rexroth being the most common. However, we have also seen Thomson Linear, INA, STAR, Hiwin, and many others. The type of ball screw assembly, its manufacturer, and the level of preventative maintenance care it has received, typically determine whether it can be rebuilt or if new components are necessary. Our team consults with customers, showing them what they have, and helping them decide on the optimal solution based on their budget and application.
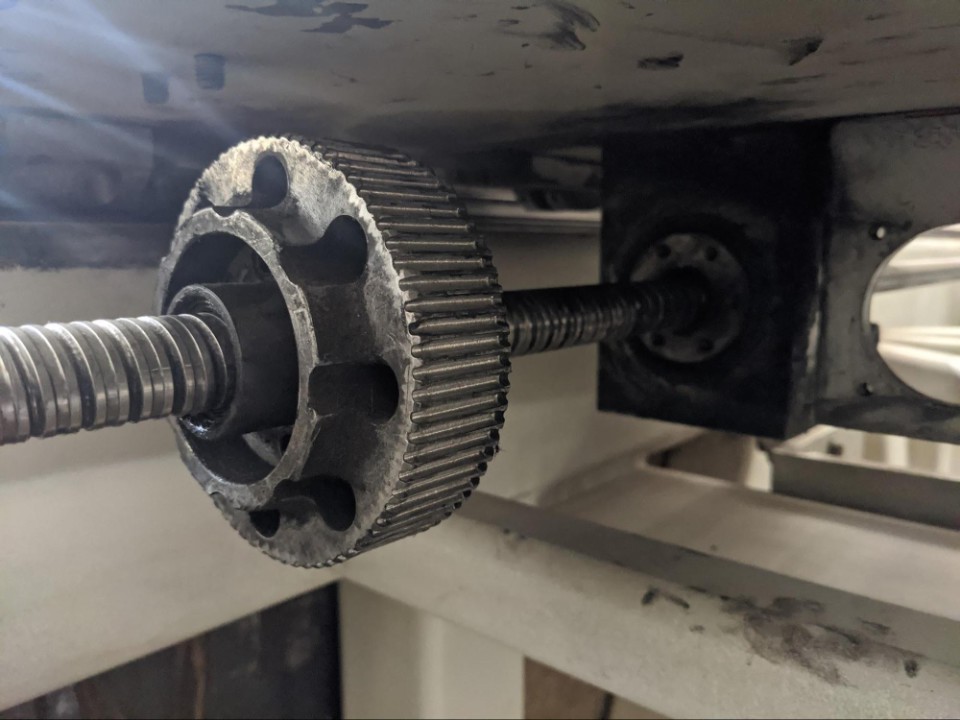
Another essential system often overlooked in Flow Water Jet X-axis service is the rotation bearing. This is an assembly mounted underneath the cutting head gantry, shown here in the shadow behind the pulley on the shaft. It is where the ball nut and pulley connect to the machine, allowing the ball nut to spin connected to the gantry as it is driven by the servo and drive belt. In most cases, this rotation bearing receives grease, as its grease fittings are typically on a bank not hidden by the X-axis covers. However, it can run and wear down over the years. Essentially, inside this unit are two angular contact bearings. As they wear down over time, they can become loose. This can manifest itself on cut parts as what appears to be backlash, even if the ball screws are just fine.
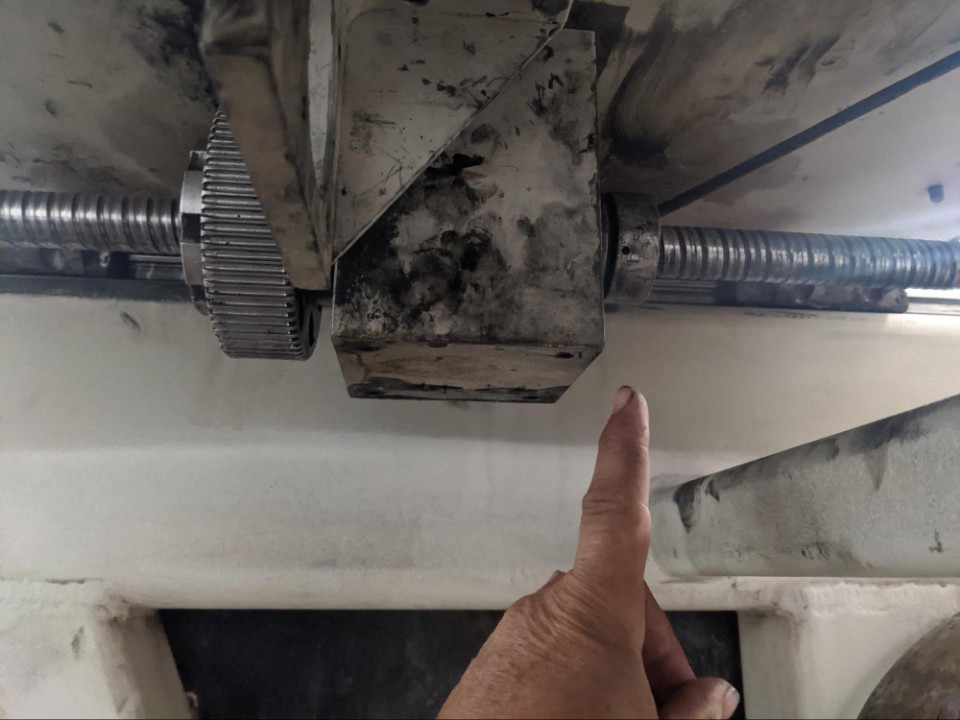
This is the side view of the X-Axis yoke and rotation bearing housing found on many Flow Water Jets. Here the servo motor is completely removed. The ball screw has been refurbished. The ball nut is installed with the drive pulley. Inside that block are a pair of angular contact bearings. These are sandwiched inside and kept in place by a threaded nut on the back end of the assembly. We verify that this bearing assembly is set at the proper contact tension. Being mindful to not crush the bearings or leave them too loose. Afterward, we reinstall the servo motor if it has been removed. Then install the belt, verifying proper belt tension.
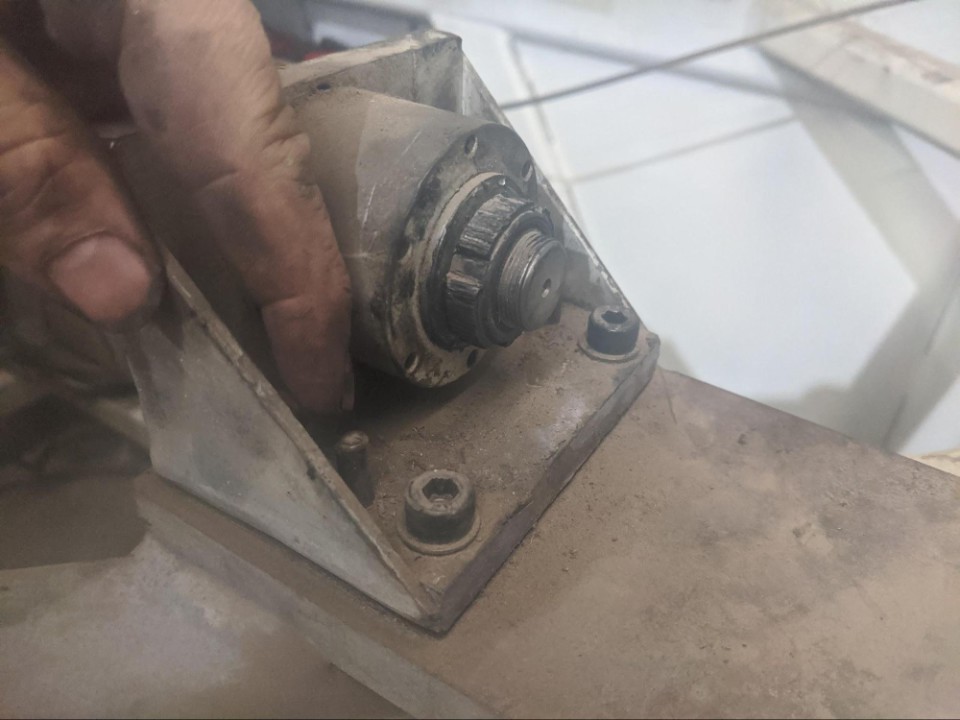
The final thing before replacing the covers and final lubrication check is to set the ball screw tension and align the end mounts to the proper centerline of rotation. The idea being that the ball screw shaft must be on a parallel plane to the linear way guides of the motion system. Also, the rotation bearing yoke housing must also be set in the same perspective elevation as the end mounts which hold the ball screw. Misalignment causes the ball nut to “crowd”, meaning the ball bearings inside are stressed unevenly within the ball nut assembly. This image was taken early in the repair process. Please forgive the dirt. We have not scrubbed it off yet in this image.